In the ever-evolving landscape of automotive manufacturing and assembly, ensuring the highest standards of quality is essential. A single overlooked detail, like an incorrect, or incorrectly seated fuse in a fuse box, can have far-reaching consequences. To tackle this challenge head-on, we offer a groundbreaking combination of technology: PEKAT VISION deep-learning vision inspection software and a Photoneo 3D scanner.
The Challenge of Fuse Box Assembly
In the automotive industry and beyond, fuses play a crucial role in ensuring the safety and functionality of electrical systems. Each fuse must be not only the correct amperage but also properly seated within its designated slot. A simple mistake during assembly can lead to electrical malfunctions, costly repairs, and even safety hazards.
Traditionally, this meticulous inspection process required significant manual labor prone to human error. Recent advancements in technology have introduced a new solution.
3D Imaging Technology
A 3D scanner is a remarkable piece of technology that captures not only the visual information of an object, the current rating or amperage of each fuse, in our case, but also their depth. This quality is important during fuse box assembly as the depth information is used to evaluate whether a fuse is fully seated in the fuse box or not.
Furthermore, Photoneo’s novel technology features a state-of-the-art 3D reconstruction of highly dynamic scenes, such as a fuse box moving on a conveyer belt.
The Role of PEKAT VISION Deep-Learning Software
PEKAT VISION steps in to make sense of the data collected by the Photoneo scanner. Its Optical Character Recognition (OCR) module comes into play to read the numbers on each fuse, ascertaining if they match the required amperage for the designated slot or not.
Based on the depth information from the scanner assigns PEKAT VISION Classifier module a corresponding class to each position/slot of the fuse box. Bellow follows a short summary of the whole process.
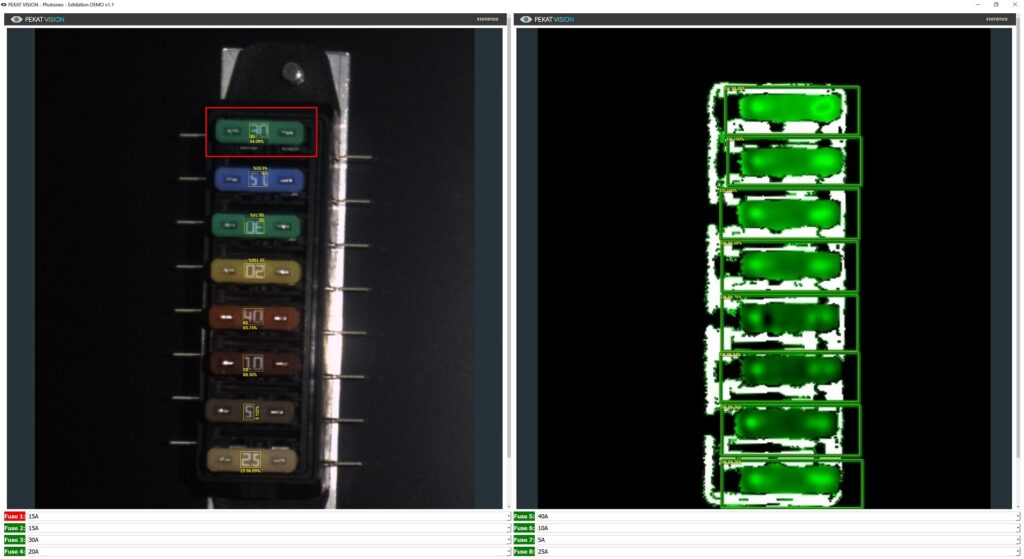
Image 1: PEKAT VISION Screen: Each slot is assessed individually, using the OCR module (left) and Classifier module (right). In this example, the first slot is fully seated, but is of different amperage than required, 30A instead of the assigned 15A (highlighted in red). Notice that the orientation of the fuse is irrelevant to the reading.
Summary of the Evaluation Process
– 3D Scanning: The Photoneo 3D scanner captures a detailed image, including the amperage and depth information of each fuse.
– OCR Reading: PEKAT VISION’s OCR module reads the amperage rating on each fuse.
– Classification: PEKAT VISION’s Classifier module assigns a class to each slot conveying the information whether each fuse is fully seated, partially seated, or missing.
– Evaluation: If both, the recognized number/ amperage and depth information for each slot convey that all fuses are correctly placed and seated, the image is evaluated as “OK”. If any fuse has incorrect amperage or is not seated properly, the image is evaluated as “NOK”. Each number that is incorrect or position that is classified as either “Empty”, or “Partially Inserted” is highlighted, triggering a corrective action.
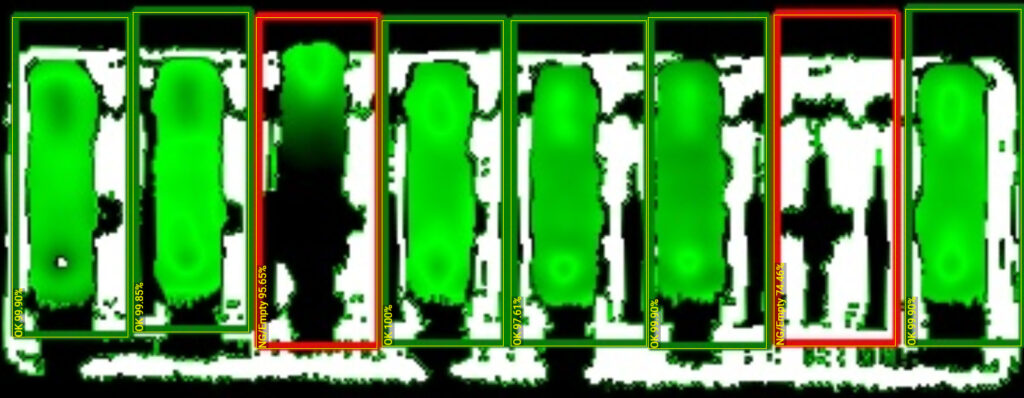
Image 2: PEKAT VISION Depth Reading: Slot 3 (from the left) evaluated as “Partially Inserted” and slot 7 as “EMPTY”. Each alone will result in the image to be evaluated as “NOK”
The Benefits of 3D imaging and Deep-learning
The integrated approach to quality control of the fuse boxes offers several notable benefits:
– Enhanced Accuracy: Human error is virtually eliminated, ensuring that each fuse is correctly seated and has the right amperage.
– Time Efficiency: The combination of 3D scanning and PEKAT VISION deep-learning data evaluation significantly reduces inspection time.
– Cost Saving: Fewer errors mean fewer warranty claims and repairs, ultimately saving manufacturers time and money
– Safety Assurance: Ensures the safety and functionality of electrical systems, reducing the risk of electrical malfunctions or safety hazards.
In conclusion, the marriage of Photoneo 3D scanning technology with PEKAT VISION deep learning software has transformed the landscape of quality control not only in fuse box assembly and the automotive sector. It is a testament to the power of innovation in manufacturing, where technology not only enhances precision but also streamlines processes, reduces costs, and, most importantly, ensures the safety and reliability of the end product.
If you would like to check whether PEKAT VISION is suitable for your particular need, please, contact us or request a free demo or feasibility study.